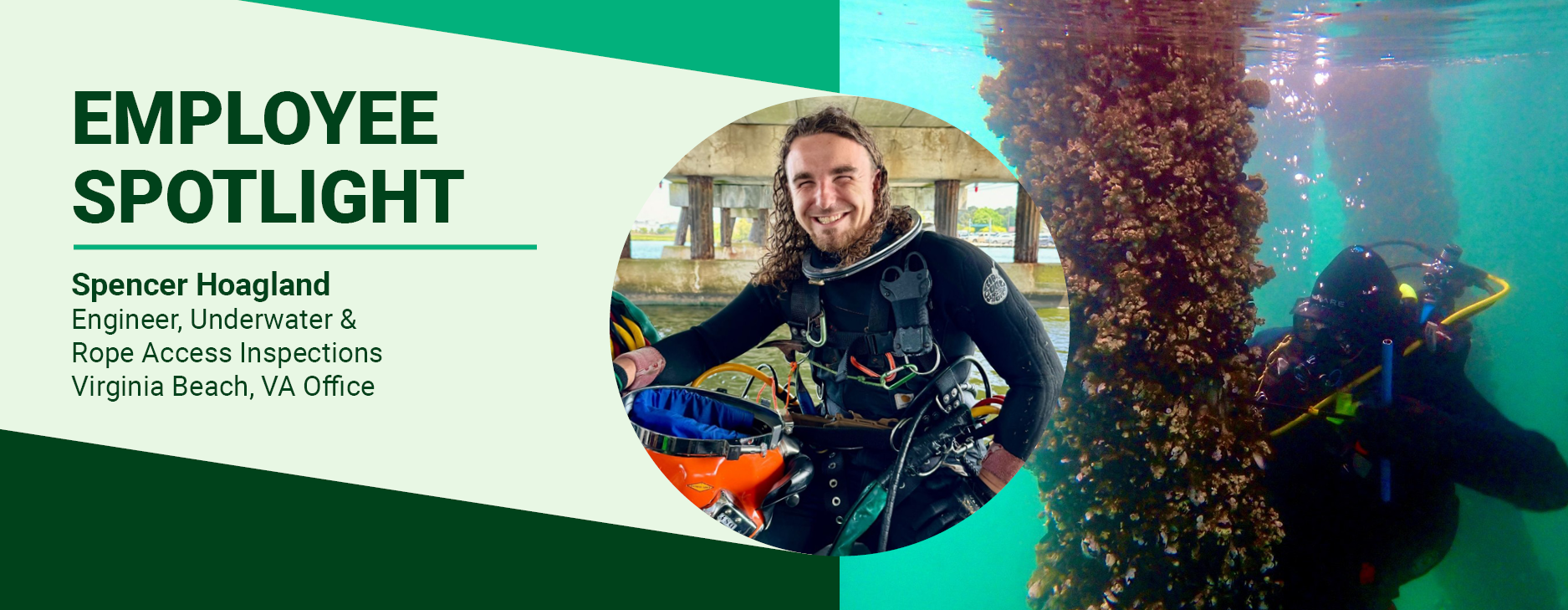
Pennoni’s Employee Spotlight series gives you a behind-the-scenes look at the talented individuals who make our company thrive. Each month, we highlight a team member’s journey, their passion for engineering and innovation, and the unique impact they’re making at Pennoni.
This month, we’re featuring Spencer Hoagland, EIT, engineer diver in our Virginia Beach, VA office and highlighting his favorite projects, showcasing his underwater diving skills and diving deep on how he overcomes engineering challenges!
Spencer is an engineer specializing in underwater and rope access inspections. Originally from Waterford, CT, Spencer grew up with a deep appreciation for engineering, inspired by his parents—both engineers at the local nuclear power plant. He pursued his passion at Worcester Polytechnic Institute (WPI), where he earned his bachelor’s in civil engineering in 2021. During a summer internship as a freshman, Spencer discovered the specialized field of engineer diving, setting his sights on a career that would merge technical problem-solving with hands-on, field-based engineering. He began his professional journey with Collins Engineers in 2021 as a bridge inspector, which brought him from New England to Virginia, and in the spring of 2023, he attended dive school in Minnesota to further develop his expertise in underwater inspections.
In July 2024, Spencer joined Pennoni after being recruited by Nate Brown for a diving position. Since then, he has been an integral part of the firm’s dive team, leveraging his skills in structural evaluation and inspection. Notably, he contributed to the inspection and load rating of the Manchester Pier in Washington, seamlessly integrating his diving abilities with his engineering knowledge. Recently, he also achieved his SPRAT certification, expanding his capabilities to perform rope access inspections on structures that require specialized climbing techniques.
Dedicated to both technical excellence and field innovation, Spencer is currently preparing for his PE exam, which he plans to take after the dive season concludes. He values the expertise and precision of the Pennoni team, from structural evaluations and report writing to the critical safety measures involved in diving and climbing. Spencer is eager to continue expanding his knowledge, refining his skills, and contributing to Pennoni’s success in these specialized fields.
Pennoni is known for tackling unique and challenging projects—what’s been the most exciting or rewarding aspect of your work here so far?
One of the most rewarding experiences I’ve had at Pennoni has been contributing to the inspection and load rating of the Manchester Pier in Washington, a historic timber structure built around World War II. Originally designed alongside a sister pier that supported a submarine net for shipyard protection, the pier now serves as a critical access point for NOAA’s offshore fishnet operations. This project was particularly meaningful because it brought together every aspect of my background—engineering, diving, and hands-on testing. I was actively involved in both the above- and underwater inspections, including timber core sampling to assess pile integrity. Back in the office, I collaborated with Will Lynes to develop a structural load rating utilizing STAAD, where I gained valuable experience in interpreting real-world field data and applying it to model structural capacity under deteriorated conditions.
This project allowed me to bridge my ADCI diver training with my engineering foundation, giving me a full-circle perspective on structural evaluation. Being engaged from fieldwork to final calculations not only deepened my technical expertise but also sharpened my skills in preparation for the PE exam, which I plan to take later this year. It’s an experience I’m especially proud to be presenting on this April in a TED Talk, showcasing how young engineers can integrate technical knowledge with field experience to make a meaningful impact.
Underwater inspections sound like something straight out of an adventure movie! Can you walk us through what it’s like to inspect a bridge below the surface?
Inspecting a bridge below the surface feels like stepping into another world—weightless, breathing through an umbilical, sometimes floating effortlessly, other times fighting the river current just to stay in position. When the helmet seals, each breath draws in a rush of air through the regulator, a reminder that I’m entering a place humans were not built to exist. Most people will never have the opportunity—or the ability—to see the world from this perspective, but with the right training, equipment, and team, it becomes possible—and, more importantly, safe. My only connection to the surface is the topside tender and the comms box operator, who monitor every detail to ensure my safety while I navigate the structure alone beneath the water. The visibility varies—sometimes I can see 5 to 10 feet, but in East Coast rivers and southern swamps, it’s often just a few inches. Stir up the sediment, and that drops to zero instantly. More often than not, the world around me is pitch black—unless my dive light is on, casting an eerie orange glow through the murk.
The submerged portions of bridges are covered in thick marine growth, with fish darting between piles and beams, creating an ecosystem most people never get to see up close. In Washington, sea lions and seals have curiously circled our inspection team; in the Southeast, alligators add another layer of unpredictability. Despite these conditions, safety is always the priority—we follow strict U.S. Navy dive tables to avoid decompression risks, and dives can last anywhere from 30 minutes to several hours depending on depth and complexity. Each inspection involves hands-on documentation, an understanding of how forces are transferred through the bridge, precise measurements, and sometimes a structural evaluation—all with the goal of protecting the public. Climbing out of the water after a successful dive—removing my helmet and taking that first breath of fresh air—always brings a sense of accomplishment. It’s demanding work, but being able to merge structural engineering with commercial diving to safeguard vital infrastructure is something I’m incredibly thankful to be part of.
You recently completed SPRAT rope access training—how does this technique enhance Pennoni’s inspection capabilities, and what was the coolest part of the training?
Completing SPRAT rope access training has added another level of versatility to the inspection capabilities we can offer at Pennoni. Rope access opens up a world of possibilities—not just for traditional bridge inspections, but for accessing hard-to-reach infrastructure in dense urban environments, such as façade of skyscrapers, counterweight systems in high-rise buildings, and confined spaces where traditional equipment cannot go. From a transportation perspective, rope access is especially valuable when working on structures that have severe deterioration or low live load ratings. In those cases, deploying heavy equipment like bucket trucks or under-bridge snoopers may not be feasible or safe. SPRAT allows us to mobilize quickly, get boots—or in this case, harnesses—on the structure, and perform hands-on, close visual inspections, even on members in tension zones or fracture-critical components. That level of access is vital for applying our structural knowledge effectively and ensuring both public safety and the longevity of major infrastructure investments.
The coolest part of the training, for me, was learning how to navigate obstacles with only the gear on my harness and the rope systems that had been set up. Whether you’re traversing from rope to rope, rigging a re-anchor mid-air, or maneuvering around an obstruction, every move requires full-body awareness and technical skill. It reminded me of being underwater during a dive—only this time I was 30 feet in the air instead of 30 feet below the surface. That kind of exposure builds not only confidence but also respect for the craft. It was challenging, humbling, and incredibly empowering all at once.
Non-destructive testing is a crucial part of ensuring infrastructure safety. What’s one method you use that people might find surprising?
One method I’ve used that people might not expect is ultrasonic testing, particularly on bridge pins on the Robert Norris Bridge or the anchor bolts for the turret of the Coleman Bridge in Virginia. These components are critical to a structure’s overall stability, and even a small internal crack or defect—especially one that has progressed since the last inspection—can significantly reduce load-carrying capacity and increase the risk of failure if left untreated. Ultrasonic testing allows us to detect these issues without damaging the material. By using a transducer to send high-frequency sound waves through the steel, we can analyze how those waves reflect and identify hidden flaws—pinpointing the location and depth with impressive accuracy.
It’s a fascinating process—using sound to “see” inside solid metal—and one of the most effective tools we have for assessing internal conditions that aren’t visible to the naked eye. This kind of testing helps us make critical decisions about whether a bridge component can remain in service or needs intervention. There’s something incredibly rewarding about using technology like this to stay ahead of potential failures and help keep the public safe.
From bridges in Virginia to structures in the U.S. Virgin Islands, your experience spans a variety of locations. What’s been your most memorable project, and why?
One of the most unforgettable projects I’ve worked on was a bridge inspection for Eastern Federal Lands deep in the swamps of Louisiana. Visibility was near zero, currents were strong, and the presence of alligators added a level of unpredictability I was not used to—especially coming from Connecticut. When a six-foot gator got too close, we had to intervene. With support from a local trapper, we removed the threat, and I ended up being the one to fish it from the water. It was a moment that reminded me just how real the risks can be.
What made the project so memorable was not just the wildlife—it was the level of focus, composure, and adaptability the situation demanded. My dad always said, “Focus, don’t fold,” and that phrase plays in my head any time the pressure’s on—diving in a high-risk environment or learning how to do new skills on rope 30’ in the air. That experience reminded me how this work pushes you beyond textbook engineering. You have to adapt to the environment, assess real-time risks, and problem-solve on the spot. Whether I’m diving in Louisiana, inspecting piers in Washington, or rigging ropes in Virginia, every site brings new variables—and I love that. It keeps me growing not just as an engineer, but as a field leader and problem solver.